3d Printing Arizona is a revolutionary manufacturing process that builds parts in thin layers at the sub-mm scale. It is a fast and effective tool for product development and can create prototypes and models in a much shorter timeframe than traditional methods.
Many 3D printing model sites offer free files. You can also use a file search engine like Yeggi to find specific types of models.
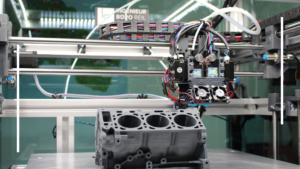
A physical prototype is an effective tool for designers to demonstrate the viability of their ideas, enabling them to avoid costly mistakes before launching into full production. In the case of a new smartphone, for example, a prototype can identify issues such as ergonomics or faulty button placement, which would be difficult to detect without a physical model. This allows the company to address these issues before launching into mass production, reducing manufacturing costs and improving user experience.
With the emergence of rapid prototyping, designers can quickly transition from digital designs to tangible prototypes. This provides an accurate and low-risk representation of the final product, allowing designers to evaluate and test the design and gather feedback from users. It also helps them to identify and prioritize improvements that will be cost-effective in the long run.
The quickest way to get your prototypes in the hands of your users is through user testing. Typically, you’ll have 7 to 30 users take a look at your prototype and provide their input. After each round of testing, you’ll analyze the results and identify key themes and trends. Then, you can make minor tweaks to your prototype and repeat the testing process until you have a clearly improved design.
Once you have your functional prototypes, the next step is to produce a “works-like” model that’s as close as possible to the final product. For this stage, it’s important to use a material that resembles the final product, which is why injection molding, CNC machining or industrial-grade 3D printing are typically used.
In addition to speeding up the development cycle and avoiding costly mistakes, having your prototypes in hand can also help you secure funding. A functioning prototype demonstrates that your concept is feasible and can be implemented, making it easier to pitch the project to potential investors or funders. This can also help you to negotiate a better deal, as investors may view the project as less risky if it has already passed the proof of concept phase. This is particularly true if you’re pitching the idea to a large investor, such as a venture capital firm.
Additive Manufacturing
Additive manufacturing (AM) is a broad term that encompasses many different types of printing technologies. It refers to the process of constructing three-dimensional physical solid objects from a digital computer-aided design (CAD) model. Additive manufacturing differs from subtractive methods of part fabrication in that it builds up a part by adding layer upon layer rather than cutting, grinding or milling away material.
This method of manufacturing allows engineers to build a product the way they visualize it, reducing the need for traditional machining constraints in the design phase. It also provides more flexibility to create lightweight geometries that can be difficult or impossible to fabricate using conventional methods.
AM technology is used in many industries for prototyping and end-use production. It is a fast and cost-effective method of producing parts that can be used for a wide range of applications. It is increasingly being adopted by medical-related industries to produce patient-specific replicas of bones, organs and blood vessels and for regenerative medicine.
Until recently, additive manufacturing was only available in the industrial sector. However, the availability of consumer-grade home 3D printers has opened up this technology to a wider audience. These printers can print a variety of polymers, including plastics and metals, and offer a high level of resolution.
These printers are easy to operate and use, making them ideal for prototyping. They are also relatively inexpensive, allowing for quick, low-cost production of complex geometric shapes and prototypes. This has enabled manufacturers to quickly make changes and test a new design before spending large amounts of money on production runs of the final product.
In addition, the cost of materials for additive manufacturing is much lower than for traditional methods, so this method is a great alternative for small- and medium-sized companies. The only downside to this type of manufacturing is that it can take a long time to complete a print, depending on the size and quality of the part being printed.
The most common use of 3D printing technology is in the field of biomedicine, where it can be used to manufacture patient-specific models for surgical guides and orthopedic implants. This is because these models can be created in a fraction of the time and at a far lower cost than conventional models, enabling doctors to perform operations with greater accuracy.
3D Printing Materials
3D printing relies on a wide range of materials for its creations. Some of the most common are plastic polymers that can be printed as solid or hollow objects. These are often used for prototyping and are available in a variety of colors and finishes. Other materials include metals, ceramics, and epoxy-based resins. These materials are often combined to create a variety of unique products.
The most popular 3D printing material is plastic, which is most commonly used for concept models and prototypes. It is a durable material that can be shaped into a number of different shapes and has the benefit of being relatively inexpensive. It is also lightweight and offers a wide color palette to suit any design.
More advanced 3D printers are capable of printing with a wide range of materials, including metal. These processes, known as direct metal laser sintering (DMLS) and selective laser melting (SLM), provide the most accurate part reproductions. The resulting parts are strong and have good surface finishes, but they can be expensive to produce. The size of the printed parts is limited to the volume of the printer’s build chamber.
In addition to reducing manufacturing time, the ability to print with multiple materials is enabling the development of complex products that would be impossible to produce by traditional methods. This multi-material printing technique has applications in medical technology, aerospace, automotive, and energy. It is also expected to make construction of new buildings more efficient, as it will eliminate the need to transport large amounts of materials to a building site and reduce the need for waste removal.
Another way that the printing process is improving is through the development of composite materials, which combine one or more plastics with other materials to enhance their performance. For example, carbon fiber is a powerful reinforcement material that can be added to plastics to produce strong, lightweight parts. This is especially useful for replacing metal parts that would otherwise require long lead times, as it can significantly reduce the weight of a product without compromising its strength.
Material Jetting
Material jetting 3D printing uses a system of print heads (similar to those in a standard 2D inkjet paper printer) that dispenses droplets of a photosensitive material which hardens under UV light, building up the object layer by layer. The most common material for this type of 3D printing is thermoset polymers such as ABS or PLA plastics, but other materials such as alumina, zirconia, waxes and various metals are also used.
The print head dispenses the liquid or powdered material onto a build platform which is heated up to allow it to fuse to the previous layer of printed material as it builds up the object. The layers are built up on top of each other until the final part is complete. The printer will then apply a coat of varnish to protect the printed item.
This is one of the fastest 3D printing technologies, and it can be printed in full color. There are a few companies who offer modified standard inkjet print heads that can be used with other materials, and enterprising do-it-yourselfers have created or modded their own 3D-capable print heads as well.
MJF is a relatively new industrial process that combines the advantages of Powder Bed Fusion with Binder Jetting technology. It is a great option for industrial prototypes and functional parts, such as tooling, jigs and fixtures, medical devices, dental aligner molds, orthotics and prosthetics, automotive components and fluid systems.
As the demand for 3D printing grows, more and more manufacturers are incorporating this revolutionary manufacturing technology into their production processes. Some are even using it as a replacement for traditional methods such as injection molding and CNC machining.
The first step in 3D printing is creating the design, which can be done in a variety of software programs ranging from expensive commercial products like AutoCAD to free and open-source options such as Google SketchUp and Blender. The resulting 3D model is stored in a file format called STL, which can be read by all of the different types of 3D printers available on the market.